Buscar este blog

lunes, 31 de octubre de 2011
jueves, 27 de octubre de 2011
Rueda inglesa
La rueda inglesa es una máquina manual para tratar plancha de metal y crear sin problemas, formas redondeadas de plancha de acero - o de aluminio.
Tiene la forma de una gran "C" cerrada con dos ruedas en los extremos. La rueda inferior suele tener un radio más pequeño que la superior. Las máquinas más grandes suelen tener la rueda superior de hasta ocho centímetros de ancho y hasta 25 de diámetro.
La rueda superior es plana, mientras que la inferior tiene una superficie redondeada. El radio de curvatura de la inferior tiene una relación muy directa con la magnitud de la curvatura que se quiera dar a la plancha, e incluso la forma final. Se dispone de una serie de perfiles diferentes para la rueda inferior, dependiendo de lo que se quiere fabricar.
El proceso consiste en hacer pasar la plancha hacia atrás y hacia adelante entre las dos ruedas. La presión entre las ruedas permite que la placa adelgace y se vaya estirando. El proceso hace que la placa vaya cogiendo forma alrededor de la rueda inferior, con su sección redonda.
La presión en el punto de contacto - que varía con el radio del perfil de la rueda inferior, la presión aplicada y el número de veces que se hace pasar la placa entre las ruedas - determina la magnitud de la deformación.Para obtener la forma que se desea, se puede cambiar mientras se trabaja entre los diferentes perfiles de rueda inferior. Conocer la combinación de las diferentes ruedas a utilizar y la presión correcta a aplicar, es un arte complejo que cuesta un tiempo relativamente largo de aprender.
Aqui vemos al ya nombrado en clase Ron Covell haciendo una demostracion de su uso.
Tiene la forma de una gran "C" cerrada con dos ruedas en los extremos. La rueda inferior suele tener un radio más pequeño que la superior. Las máquinas más grandes suelen tener la rueda superior de hasta ocho centímetros de ancho y hasta 25 de diámetro.
La rueda superior es plana, mientras que la inferior tiene una superficie redondeada. El radio de curvatura de la inferior tiene una relación muy directa con la magnitud de la curvatura que se quiera dar a la plancha, e incluso la forma final. Se dispone de una serie de perfiles diferentes para la rueda inferior, dependiendo de lo que se quiere fabricar.
El proceso consiste en hacer pasar la plancha hacia atrás y hacia adelante entre las dos ruedas. La presión entre las ruedas permite que la placa adelgace y se vaya estirando. El proceso hace que la placa vaya cogiendo forma alrededor de la rueda inferior, con su sección redonda.
La presión en el punto de contacto - que varía con el radio del perfil de la rueda inferior, la presión aplicada y el número de veces que se hace pasar la placa entre las ruedas - determina la magnitud de la deformación.Para obtener la forma que se desea, se puede cambiar mientras se trabaja entre los diferentes perfiles de rueda inferior. Conocer la combinación de las diferentes ruedas a utilizar y la presión correcta a aplicar, es un arte complejo que cuesta un tiempo relativamente largo de aprender.
Aqui vemos al ya nombrado en clase Ron Covell haciendo una demostracion de su uso.
Varilleros
Los varilleros son chapistas o carroceros que mediante una tecnica poco frecuente y hasta hace poco secreta son capaces de extraer pequeños abollones sin necesidad de volver a pintar el coche. Esto lo hacen aplicando presion con unas varillas sobre puntos estrategicos de abolladuras provocadas basicamente por granizo u otros golpes leves como golpes con otra puerta etc. En este video vemos una demostracion.
Oxidación y corrosión
Estos dos términos pueden parecer lo mismo pero no es asi. Cuando hablamos de oxidación tenemos que hablar de dos tipos de oxidos, los permeables y los impermeables. Oxidos impermeables son por ejemplo la alumina ( oxido de aluminio ). Este material es duro y como habiamos dicho impermeable, crea una capa que aisla el interior de la pieza de aluminio con el aire exterior. Con esto paramos la reaccion del aluminio con el oxigeno ya que deja de entrar en contacto con él. Por otro lado estan los oxidos permeables como el oxido ferrico/ferroso. Es un polvillo exterior que forma cavidades en el exterior de la pieza de hierro y con el mismo aire ese polvo que podria protejer el resto de hierro se va y vuelve a oxidarse el hierro. Por lo tanto se deteriora. Ademas dentro de esas cavidades se queda acumulado aire con su correspondiente humedad, la cual favorecera la corrosión.
Cuando hablamos de hierro hablamos de aceros tambien. Dentro de estos aceros encontramos los inoxidables, un tipo de acero que vulgarmente se dice que no se oxida, pero si se oxida. Precisamente es el oxido el que proteje el interior de la pieza, pero es el oxido del cromo de la aleacion el que proteje al hierro. Digamos que ese oxido es como la alumina, que una vez creado proteje el resto de la pieza. Lo que nunca sufrira una pieza de acero inoxidable es corroerse.
Cuando hablamos de hierro hablamos de aceros tambien. Dentro de estos aceros encontramos los inoxidables, un tipo de acero que vulgarmente se dice que no se oxida, pero si se oxida. Precisamente es el oxido el que proteje el interior de la pieza, pero es el oxido del cromo de la aleacion el que proteje al hierro. Digamos que ese oxido es como la alumina, que una vez creado proteje el resto de la pieza. Lo que nunca sufrira una pieza de acero inoxidable es corroerse.
sábado, 22 de octubre de 2011
El cobre, caracteristicas.
Biocida
El cobre también es útil como biocida. Es algo que podemos utilizar para controlar las plagas de insectos. Para las plantas, se utiliza a menudo para eliminar los hongos que crecen en sus hojas. Puede usarse para acabar con las bacterias e insectos que dañan las cosechas de los granjeros. También se utiliza para el cuidado de las vides productoras de uvas para vino.
Propiedades físicas
Propiedades mecánicas
Tanto el cobre como sus aleaciones tienen una buena maquinabilidad, es decir, son fáciles de mecanizar. El cobre posee muy buena ductilidad y maleabilidad lo que permite producir láminas e hilos muy delgados y finos. Es un metal blando, con un índice de dureza 3 en la escala de Mohs (50 en la escala de Vickers) y su resistencia a la tracción es de 210 MPa, con un límite elástico de 33,3 MPa.[3] Admite procesos de fabricación de deformación como laminación o forja, y procesos de soldadura y sus aleaciones adquieren propiedades diferentes con tratamientos térmicos como temple y recocido. En general, sus propiedades mejoran con bajas temperaturas lo que permite utilizarlo en aplicaciones criogénicas
Características químicas
En la mayoría de sus compuestos, el cobre presenta estados de oxidación bajos, siendo el más común el +2, aunque también hay algunos con estado de oxidación +1.
Expuesto al aire, el color rojo salmón inicial se torna rojo violeta por la formación de óxido cuproso (Cu2O) para ennegrecerse posteriormente por la formación de óxido cúprico (CuO).] La coloración azul del Cu+2 se debe a la formación del ion [Cu (OH2)6]+2.
Expuesto largo tiempo al aire húmedo, forma una capa adherente e impermeable de carbonato básico (carbonato cúprico) de color verde y venenoso.También pueden formarse pátinas de cardenillo, una mezcla venenosa de acetatos de cobre de color verdoso o azulado que se forma cuando los óxidos de cobre reaccionan con ácido acético, que es el responsable del sabor del vinagre y se produce en procesos de fermentación acética. Al emplear utensilios de cobre para la cocción de alimentos, deben tomarse precauciones para evitar intoxicaciones por cardenillo que, a pesar de su mal sabor, puede ser enmascarado con salsas y condimentos y ser ingerido.
Precio
Su amplio rango de usos hace que el cobre sea un material muy cotizado. No podemos dar una cifra exacta euros/kg pero es alta. Mucha gente se dedica a su recogida y propicia muchos robos, un problema muy actual.
ALCOA

Alcoa (NYSE: AA) es una empresa estadounidense, la más grande productora de aluminio en el mundo.
Establecida en Pittsburgh, Pensilvania en 1888, adoptó el nombre de Aluminum Co. of America en 1907, del cual se deriva el mote actual. Alcoa introdujo el papel aluminio en 1910 y encontró usos para el aluminio en las incipientes industrias de aviación y del automóvil.
En 1913 estableció la localidad de Alcoa al Este de Tennessee como una comunidad industrial. Una normativa federal antimonopolio de 1945, obligó a la empresa a vender su filial canadiense (hoy en día Alcan Aluminum Ltd., su más fuerte competidor). En 1998 Alcoa adquirió Alumax Inc., una empresa productora de contenedores plásticos y equipamiento de embalaje. Asimismo en 1998 adquirió la mayor parte de los recursos de la empresa del INI dedicada a la fabricación de aluminio Inespal (centros de producción en San Ciprian, Coruña, Avilés, Amorebieta, Alicante, Sabiñánigo y Noblejas )
Algún producto Alcoa relacionado con la automoción.

Llanta de camión.
TRATAMIENTOS
Aqui publico unos cuantos tratamientos del acero.
Temple: Su finalidad es aumentar la dureza y la resistencia del acero. Para ello, se calienta el acero a una temperatura ligeramente más elevada que la crítica superior Ac (entre 900-950 °C) y se enfría luego más o menos rápidamente (según características de la pieza) en un medio como agua, aceite, etcétera.
Revenido: Sólo se aplica a aceros previamente templados, para disminuir ligeramente los efectos del temple, conservando parte de la dureza y aumentar la tenacidad. El revenido consigue disminuir la dureza y resistencia de los aceros templados, se eliminan las tensiones creadas en el temple y se mejora la tenacidad, dejando al acero con la dureza o resistencia deseada. Se distingue básicamente del temple en cuanto a temperatura máxima y velocidad de enfriamiento.
Recocido: Consiste básicamente en un calentamiento hasta temperatura de austenitización (800-925 °C) seguido de un enfriamiento lento. Con este tratamiento se logra aumentar la elasticidad, mientras que disminuye la dureza. También facilita el mecanizado de las piezas al homogeneizar la estructura, afinar el grano y ablandar el material, eliminando la acritud que produce el trabajo en frío y las tensiones internas.
Normalizado: Tiene por objeto dejar un material en estado normal, es decir, ausencia de tensiones internas y con una distribución uniforme del carbono. Se suele emplear como tratamiento previo al temple y al revenido.
Cementación (C): aumenta la dureza superficial de una pieza de acero dulce, aumentando la concentración de carbono en la superficie. Se consigue teniendo en cuenta el medio o atmósfera que envuelve el metal durante el calentamiento y enfriamiento. El tratamiento logra aumentar el contenido de carbono de la zona periférica, obteniéndose después, por medio de temples y revenidos, una gran dureza superficial, resistencia al desgaste y buena tenacidad en el núcleo.
Nitruración (N): al igual que la cementación, aumenta la dureza superficial, aunque lo hace en mayor medida, incorporando nitrógeno en la composición de la superficie de la pieza. Se logra calentando el acero a temperaturas comprendidas entre 400 y 525 °C, dentro de una corriente de gas amoníaco, más nitrógeno.
Cianuración (C+N): endurecimiento superficial de pequeñas piezas de acero. Se utilizan baños con cianuro, carbonato y cianato sódico. Se aplican temperaturas entre 760 y 950 °C.
Carbonitruración (C+N): al igual que la cianuración, introduce carbono y nitrógeno en una capa superficial, pero con hidrocarburos como metano, etano o propano; amoníaco (NH3) y monóxido de carbono (CO). En el proceso se requieren temperaturas de 650 a 850 °C y es necesario realizar un temple y un revenido posterior.
Sulfinización (S+N+C): aumenta la resistencia al desgaste por acción del azufre. El azufre se incorporó al metal por calentamiento a baja temperatura (565 °C) en un baño de sales.
Forja : es un proceso de conformado por deformación plástica que puede realizarse en caliente o en frío y en el que la deformación del material se produce por la aplicación de fuerzas de compresión.
Forja : es un proceso de conformado por deformación plástica que puede realizarse en caliente o en frío y en el que la deformación del material se produce por la aplicación de fuerzas de compresión.
Escoria.
Las escorias son un subproducto de la fundición de la mena para purificar los metales. Se pueden considerar como una mezcla de óxidos metálicos; sin embargo, pueden contener sulfuros de metal y átomos de metal en forma de elemento. Aunque la escoria suele utilizarse como un mecanismo de eliminación de residuos en la fundición del metal, también pueden servir para otros propósitos, como ayudar en el control de la temperatura durante la fundición y minimizar la reoxidación del metal líquido final antes de pasar al molde.
En la naturaleza, los minerales de metales como el hierro, el cobre, el aluminio y otros metales se encuentran en estados impuros, a menudo oxidados y mezclados con silicatos de otros metales.
Durante la fundición, cuando la mena está expuesta a altas temperaturas, estas impurezas se separan del metal fundido y se pueden retirar. La colección de compuestos que se retira es la escoria.
Usos:
La escoria tiene muchos usos comerciales y raramente se desecha. A menudo se vuelve a procesar para separar algún otro metal que contenga. Los restos de esta recuperación se pueden utilizar como balasto para el ferrocarril y como fertilizante. Se ha utilizado como metal para pavimentación y como una forma barata y duradera de fortalecer las paredes inclinadas de los rompeolas para frenar el movimiento de las olas.
A menudo se utiliza escoria granular de alto horno en combinación con el mortero de cemento pórtland como parte de una mezcla de cemento. Este tipo de escoria reacciona con el agua para producir propiedades cementosas. El mortero que contiene escoria granular de alto horno desarrolla una gran resistencia durante largo tiempo, ofreciendo una menor permeabilidad y mayor durabilidad. Como también se reduce la unidad de volumen de cemento pórtland, el mortero es menos vulnerable al álcali-sílice y al ataque de sulfato.
En la naturaleza, los minerales de metales como el hierro, el cobre, el aluminio y otros metales se encuentran en estados impuros, a menudo oxidados y mezclados con silicatos de otros metales.
Durante la fundición, cuando la mena está expuesta a altas temperaturas, estas impurezas se separan del metal fundido y se pueden retirar. La colección de compuestos que se retira es la escoria.
Usos:
La escoria tiene muchos usos comerciales y raramente se desecha. A menudo se vuelve a procesar para separar algún otro metal que contenga. Los restos de esta recuperación se pueden utilizar como balasto para el ferrocarril y como fertilizante. Se ha utilizado como metal para pavimentación y como una forma barata y duradera de fortalecer las paredes inclinadas de los rompeolas para frenar el movimiento de las olas.
A menudo se utiliza escoria granular de alto horno en combinación con el mortero de cemento pórtland como parte de una mezcla de cemento. Este tipo de escoria reacciona con el agua para producir propiedades cementosas. El mortero que contiene escoria granular de alto horno desarrolla una gran resistencia durante largo tiempo, ofreciendo una menor permeabilidad y mayor durabilidad. Como también se reduce la unidad de volumen de cemento pórtland, el mortero es menos vulnerable al álcali-sílice y al ataque de sulfato.
Carbón de coque, indispensable en la fabricacion de aceros y fundiciones.
CARBÓN DE COQUE
El coque es un combustible obtenido de la destilación de la hulla calentada a temperaturas muy altas en hornos cerrados y a la cual añaden calcita para mejorar su combustión, que la aíslan del aire, y que sólo contiene una pequeña fracción de las materias volátiles que forman parte de la misma. Es producto de la descomposición térmica de carbones bituminosos en ausencia de aire. Cuando la hulla se calienta desprende gases que son muy útiles industrialmente; el sólido resultante es el carbón de coque, que es liviano y poroso.
Durante la revolución industrial sustituyó al carbón vegetal como reductor y fuente de energía en los altos hornos, facilitando el desarrollo de la industria siderúrgica, que dependía hasta entonces de un recurso muy limitado como es la leña. Su empleo se popularizó para la calefacción de hogares, pues su combustión no produce humo y es menos contaminante. El carbón de coque es un combustible muy importante para la fabricación del hierro y del acero.
El coque es producido en una instalación llamada batería de coque, constituida por una serie de hornos en batería. El proceso de transformación de la hulla en coque, conocido como coquizado, consiste en su horneado durante un tiempo de entre 10 y 24 horas, dependiendo del tamaño del horno. Durante el coquizado se desprenden una serie de gases y líquidos de gran utilidad industrial, hecho por el que muchas plantas procesadoras de coque se centran más en los subproductos que en el propio coque, vendiendo éste a precio de costo.
Para la introducción del carbón en el horno, se utilizan carros de carga, cuya función consiste en transportar el carbón desde las torres de carga, abrir las tapas del horno e introducirlo en él. Durante la carga de un horno otra máquina, la deshornadora, se encarga de alisar o allanar el carbón que se va introduciendo en él, evitando la formación de grandes taludes en su interior. La deshornadora, como su nombre indica, sirve también para extraer el coque del horno, empujando todo el contenido sobre una máquina locomotora, encargada de recoger y desplazar el coque producido. Todo este proceso conlleva un alto riesgo, ya que se pueden producir sobrepresiones o depresiones en el interior de los hornos, por lo que el control de la temperatura, de la presión y de los gases es un factor fundamental en estas instalaciones.
El coque es un combustible obtenido de la destilación de la hulla calentada a temperaturas muy altas en hornos cerrados y a la cual añaden calcita para mejorar su combustión, que la aíslan del aire, y que sólo contiene una pequeña fracción de las materias volátiles que forman parte de la misma. Es producto de la descomposición térmica de carbones bituminosos en ausencia de aire. Cuando la hulla se calienta desprende gases que son muy útiles industrialmente; el sólido resultante es el carbón de coque, que es liviano y poroso.
Durante la revolución industrial sustituyó al carbón vegetal como reductor y fuente de energía en los altos hornos, facilitando el desarrollo de la industria siderúrgica, que dependía hasta entonces de un recurso muy limitado como es la leña. Su empleo se popularizó para la calefacción de hogares, pues su combustión no produce humo y es menos contaminante. El carbón de coque es un combustible muy importante para la fabricación del hierro y del acero.
El coque es producido en una instalación llamada batería de coque, constituida por una serie de hornos en batería. El proceso de transformación de la hulla en coque, conocido como coquizado, consiste en su horneado durante un tiempo de entre 10 y 24 horas, dependiendo del tamaño del horno. Durante el coquizado se desprenden una serie de gases y líquidos de gran utilidad industrial, hecho por el que muchas plantas procesadoras de coque se centran más en los subproductos que en el propio coque, vendiendo éste a precio de costo.
Para la introducción del carbón en el horno, se utilizan carros de carga, cuya función consiste en transportar el carbón desde las torres de carga, abrir las tapas del horno e introducirlo en él. Durante la carga de un horno otra máquina, la deshornadora, se encarga de alisar o allanar el carbón que se va introduciendo en él, evitando la formación de grandes taludes en su interior. La deshornadora, como su nombre indica, sirve también para extraer el coque del horno, empujando todo el contenido sobre una máquina locomotora, encargada de recoger y desplazar el coque producido. Todo este proceso conlleva un alto riesgo, ya que se pueden producir sobrepresiones o depresiones en el interior de los hornos, por lo que el control de la temperatura, de la presión y de los gases es un factor fundamental en estas instalaciones.
Propiedades de los materiales.
Para comprobar las propiedades de los materiales hay diversos ensayos y de los cuales obtenemos la informacion necesaria para analizar ese material. He aqui algun ejemplo.
Ensayo de resiliencia:
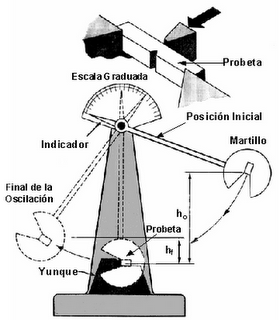
Ensayo de dureza:
(Aqui tenemos la maquina para determinar la dureza )

Ensayo de tracción:

El acero, infinitas combinaciones de Fe y C.
Se entiende por acero la aleación de hierro y carbono en la que el porcentaje de carbono no supera el 2% en peso. Porcentajes mayores que el 2% de carbono dan lugar a las fundiciones y aleaciones con muy pequeña cantidad de carbono se denominan hierro dulce o simplemente hierro. La diferencia fundamental entre ellos es que los aceros son, por su ductilidad, fácilmente deformables en caliente bien por forja, laminación o extrusión, mientras que las fundiciones se fabrican generalmente por moldeo —de hecho al acero también se le ha venido conociendo como «hierro forjable» y a la fundición «hierro colado» en virtud de la técnica más favorable para trabajar el material—; igualmente el acero se distingue del hierro dulce en que aquél puede templarse adquiriendo extraordinaria dureza mientras que el hierro dulce (blando y dúctil aunque resistente) no puede endurecerse mediante dicho procedimiento, incluso a este estado endurecido del acero se le llamó y aún llama «acritud» por contraposición a la «dulzura» natural del hierro.
La definición anterior, sin embargo, se circunscribe a los aceros al carbono en los que éste último es el único aleante o los demás presentes lo están en cantidades muy pequeñas —insuficientes para que su presencia cause modificaciones en las características de la aleación— pues de hecho existen multitud de tipos de acero con composiciones muy diversas que reciben denominaciones específicas en virtud ya sea de los elementos que predominan en su composición (aceros al silicio), de su susceptibilidad a ciertos tratamientos (aceros de cementación), de alguna característica potenciada (aceros inoxidables) e incluso en función de su uso (aceros estructurales). Usualmente estas aleaciones de hierro se engloban bajo la denominación genérica de aceros especiales, razón por la que aquí se ha adoptado la definición de los comunes o "al carbono" que amén de ser los primeros fabricados y los más empleados], sirvieron de base para los demás. Esta gran variedad de aceros llevó a Siemens a definir el acero como «un compuesto de hierro y otra sustancia que incrementa su resistencia».
Además de los componentes principales indicados, los aceros incorporan otros elementos químicos, algunos perjudiciales, provenientes de la chatarra, el mineral o el combustible empleado en el proceso de fabricación, como el azufre y el fósforo, mientras que otros se añaden intencionalmente para la mejora de alguna de las características del acero, bien para incrementar la resistencia, ductilidad, dureza, etc. o para facilitar algún proceso de fabricación como puede ser el mecanizado; tal es el caso de los elementos de aleación como el níquel, el cromo, el molibdeno, etc.
El acero es actualmente la más importante aleación mecánica empleandose de forma intensiva en numerosas aplicaciones como bienes de equipo (máquina-herramienta), construcción, etc., sin embargo, su utilización se ve condicionada en determinadas aplicaciones por las ventajas técnicas que ofrecen otros materiales como el aluminio en el transporte por su mayor ligereza y en la construcción por su mayor resistencia a la corrosión, el hormigón (aunque combinado con el acero) por su mayor resistencia al fuego, los materiales cerámicos en aplicaciones a altas temperaturas, etc.
Aún así sigue hoy día empleándose por su neta superioridad frente al resto de las aleaciones si se considera el factor precio, ya que:
Diagrama Fe-C:
La definición anterior, sin embargo, se circunscribe a los aceros al carbono en los que éste último es el único aleante o los demás presentes lo están en cantidades muy pequeñas —insuficientes para que su presencia cause modificaciones en las características de la aleación— pues de hecho existen multitud de tipos de acero con composiciones muy diversas que reciben denominaciones específicas en virtud ya sea de los elementos que predominan en su composición (aceros al silicio), de su susceptibilidad a ciertos tratamientos (aceros de cementación), de alguna característica potenciada (aceros inoxidables) e incluso en función de su uso (aceros estructurales). Usualmente estas aleaciones de hierro se engloban bajo la denominación genérica de aceros especiales, razón por la que aquí se ha adoptado la definición de los comunes o "al carbono" que amén de ser los primeros fabricados y los más empleados], sirvieron de base para los demás. Esta gran variedad de aceros llevó a Siemens a definir el acero como «un compuesto de hierro y otra sustancia que incrementa su resistencia».
Además de los componentes principales indicados, los aceros incorporan otros elementos químicos, algunos perjudiciales, provenientes de la chatarra, el mineral o el combustible empleado en el proceso de fabricación, como el azufre y el fósforo, mientras que otros se añaden intencionalmente para la mejora de alguna de las características del acero, bien para incrementar la resistencia, ductilidad, dureza, etc. o para facilitar algún proceso de fabricación como puede ser el mecanizado; tal es el caso de los elementos de aleación como el níquel, el cromo, el molibdeno, etc.
El acero es actualmente la más importante aleación mecánica empleandose de forma intensiva en numerosas aplicaciones como bienes de equipo (máquina-herramienta), construcción, etc., sin embargo, su utilización se ve condicionada en determinadas aplicaciones por las ventajas técnicas que ofrecen otros materiales como el aluminio en el transporte por su mayor ligereza y en la construcción por su mayor resistencia a la corrosión, el hormigón (aunque combinado con el acero) por su mayor resistencia al fuego, los materiales cerámicos en aplicaciones a altas temperaturas, etc.
Aún así sigue hoy día empleándose por su neta superioridad frente al resto de las aleaciones si se considera el factor precio, ya que:
- Existen numerosos yacimientos de minerales de hierro suficientemente ricos, puros y fáciles de explotar, además de la posibilidad de reciclar la chatarra.
- Los procedimientos de fabricación son relativamente simples y económicos.
- Presentan una interesante combinación de propiedades mecánicas que pueden modificarse dentro de un amplio rango variando los componentes de la aleación y sus cantidades, o mediante la aplicación de tratamientos térmicos, químicos y mecánicos.
- Su plasticidad permite obtener piezas de formas geométricas complejas con realtiva facilidad y,
- La experiencia acumulada en su utilización permite realizar predicciones de su comportamiento, reduciendo costes de diseño y plazos de puesta en el mercado.
Diagrama Fe-C:

¿ Cuál es la diferencia entre vidrio y cristal ?
Vamos a hablar ahora de una diferencia básica entre el vidrio y el cristal y que a la vez condiciona el resto de diferencias, y que no es otra que la presencia del cristal en la naturaleza (solo el cristal).


Como hemos dicho, el cristal se encuentra en la naturaleza de diferentes formas, tales como el cuarzo o el cristal de roca mientras que el vidrio es el resultado de la fusion de ciertos materiales como el silice, la sosa, la cal o el oxido de plomo, imitando siempre al cristal natural. Pero ojo, siempre hay excepciones, ya que existen vidrios creados en la naturaleza, como la obsidiana que se forma por el calor y los "detritos" generados en el interior de los volcanes. El cristal es homogéneo, osea, posee una estructura molecular simétrica y ordenada, confiriéndole así un aspecto “cristalino” y transparente, mientras que el vidrio tiene una estructura totalmente contraria a ésta.
Estructura molecular perfectamente ordenada en el caso del cristal.
¿ Qué espero de la asignatura EAF y los profesores ?
Pues a final de año espero tener una buena habilidad y conocimientos sobre el tema del que trata. Tener la capacidad de diagnosticar y resolver un problema de cualquier coche y además disfrutar con ello. Sobre vosotros los profesores lo primero llevarme bien, cosa que cuesta poco porque las clases las haceis muy amenas a pesar de ser de 3h y después poder hacer lo que pedís para poder aprobar.
Suscribirse a:
Entradas (Atom)